How Salcobrand Transformed its Supply Chain with Logmore, Enhancing Visibility and Compliance in the Distribution Process.
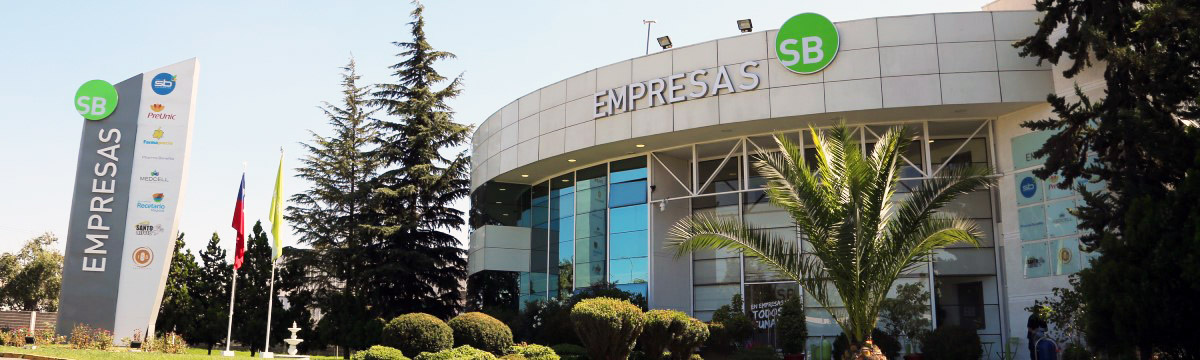
1.
Situation
Salcobrand
The Salcobrand Distribution Center, supplying one of the largest pharmacy chains in Chile, was opened in 2018, positioning itself as one of the most technologically advanced operational facilities in the pharmaceutical industry.
With a high storage capacity in racks and shelves and 29.000 square meters of construction, the distribution center carries out its logistical operations with the efforts of over 350 employees. All of them operate under the guiding principle of Quality, united by the shared mission that drives Empresas SB, the parent company of Salcobrand: "We make people feel good wherever they are, delivering the best in health, beauty, and well-being" This enables the supply of 430 pharmacies from Arica to Punta Arenas, including Easter Island and Juan Fernandez.
While its facilities represent a shift towards process automation and innovation, in terms of infrastructure and systems, Salcobrand Distribution Center is always striving for operational excellence and regulatory compliance. That is why in 2023, they embarked on a new mission: to join forces with Logmore to optimize the supply chain for products subject to cold chain requirements. To accomplish this, the different logistics and regulatory support functions provided essential assistance to achieve success.
Situation
Facing the stringent regulations for the storage, transportation, and distribution of pharmaceutical products in Chile (Technical Standards NT 147 and 208), Salcobrand encountered significant logistical challenges. These regulations mandate traceability of temperature from distribution centers to retail outlets, which must always be available for review in order to guarantee the safety of the people who use the medication.
The requirement to distribute products throughout Chile, including remote locations, increases the complexity of retrieving and analyzing shipment temperature data.
Salcobrand highlighted their need for a solution that streamlines the logistics chain by eliminating manual processes, enhancing efficiency, and ensuring no temperature data is lost during the transportation of cold chain products.
"...We were looking for an innovative solution that would provide us with absolute traceability of our operations, eliminating unnecessary manual processes in the supply chain, increasing efficiency and reducing risks within the process" Pharm. Sergio Correa, Coordinator of Regulatory Affairs at Salcobrand
2.
Solution
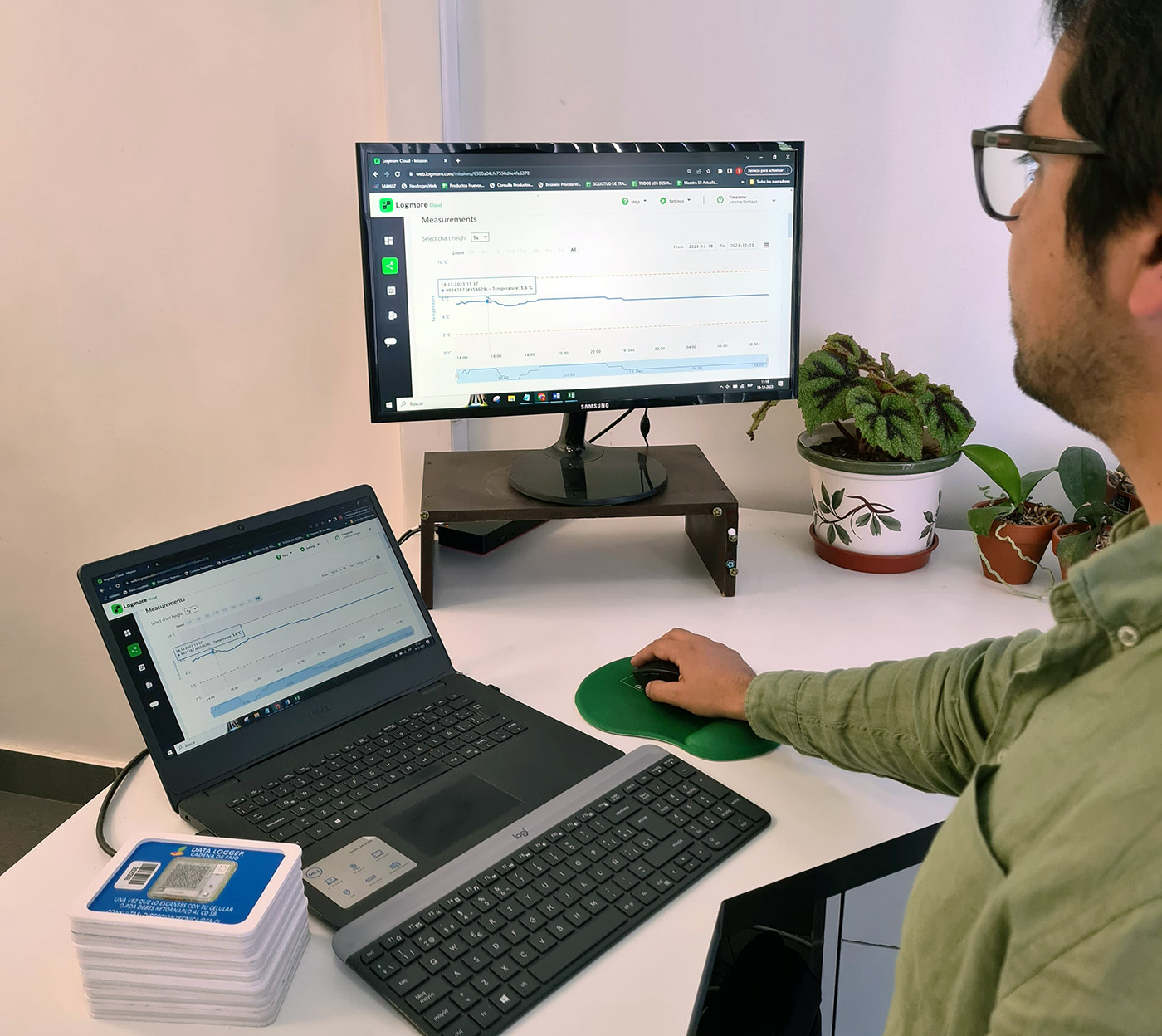
Salcobrand experienced a remarkable transformation in their operations by integrating Logmore's QR data loggers and Logmore Cloud with their Enterprise Resource Planning (ERP) system.
With the API integration, Salcobrand’s ERP system can automatically create shipments to the Logmore Cloud when a Logmore logger is selected into a shipment. At the distribution center, just the logger’s ID number is scanned into a data field for each shipment and the temperature thresholds and other settings are set fully automatically. This ensures all the data is always captured and the process is extremely straightforward at the dispatch locations.
Added value is created by the easy reusability of the Logmore loggers. The loggers are returned to the distribution center and then taken again into use without need to do any extra reconfiguration work. This is not only cost-effective but also sustainable and time saving when the same fleet of loggers can be used to monitor a great number of shipments.
With Logmore implemented in all temperature controlled shipments the process at the receiving retail locations is also improved. The Pharmacists scan the QR code of the logger for the received shipment and they’ll see instructions directly on their phone. This not only makes it easy and secure to collect the data, but also helps everyone to follow the standard operating procedures in the fast-paced environment.
"The implementation of Logmore has been an innovative experience, not only for generating the traceability we now have throughout the entire process flow but also for its integration with the ease of use of the devices and platform." - Pharm. Diego Castillo, Supplementary Technical Director at Salcobrand.
With an innovative approach, Salcobrand has successfully integrated Logmore's data loggers into its operations. These devices have not only streamlined data collection but have also proven to be essential in key activities such as temperature mapping of areas and equipment, monitoring storage areas, and route tracking. The versatility of the solution enables efficient analysis of the gathered information, providing Salcobrand with a strategic advantage in its daily operations.
Before implementing Logmore, Salcobrand faced challenges in timely information retrieval from remote locations, jeopardising full compliance with regulatory requirements. With Logmore, the company easily accesses information by simply scanning QR codes at the destination. The implementation was swift, streamlining the data download process and ensuring continuity of operations with broad acceptance across all locations.
“As the responsible for reception, I highlight the exceptional simplicity provided by Logmore. With just one scan, we can ensure that the cold chain has been effectively maintained. This functionality has significantly streamlined our processes, providing us with greater efficiency and peace of mind in the management of our products”. Pamela Uribe, Pharmacist Outlet store 733 Jumbo Costanera Center - Santiago de Chile
3.
Results
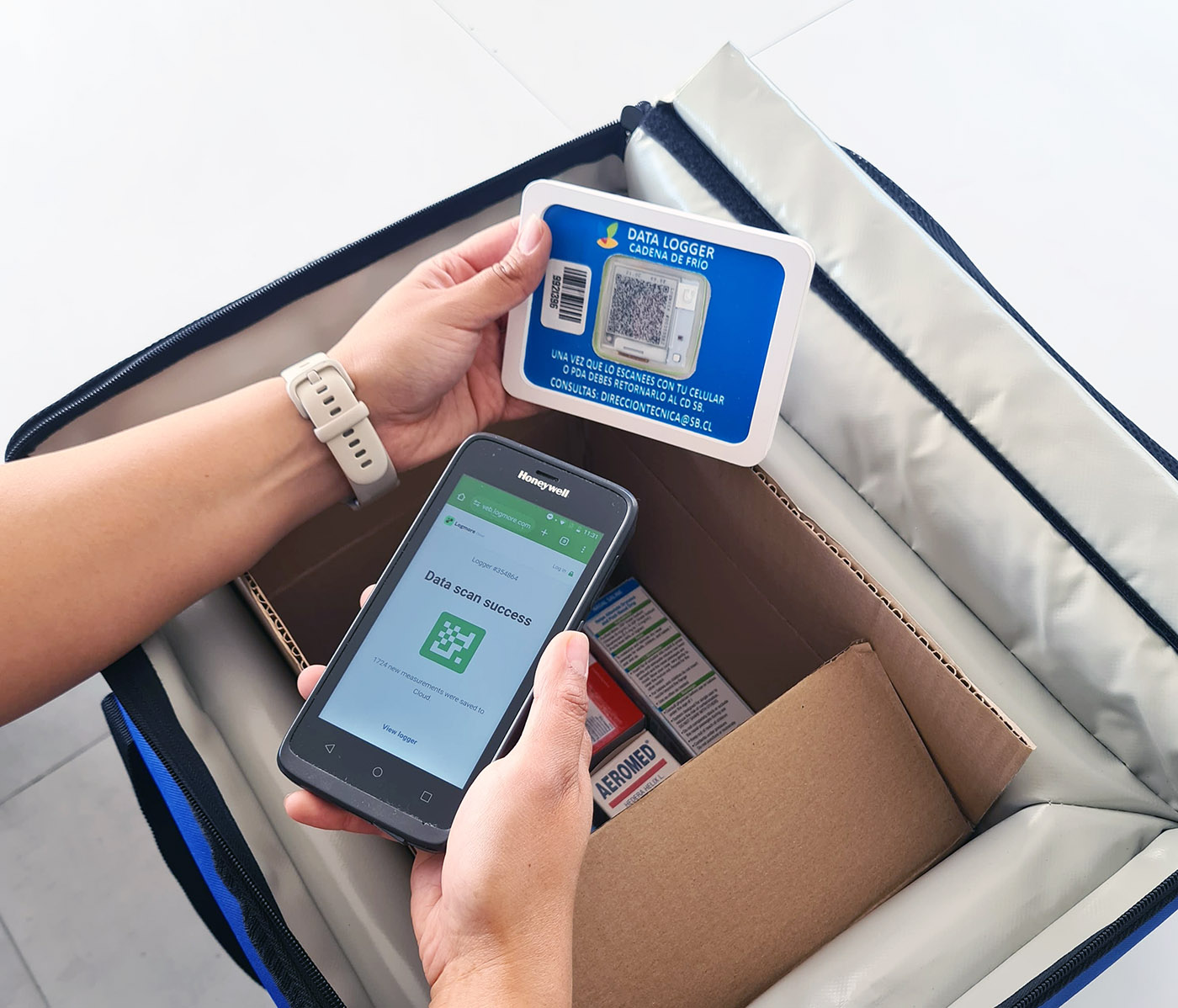
Salcobrand's implementation of Logmore's QR data loggers has led to a substantial enhancement in their logistics and supply chain management. Key improvements include:
- Complete traceability:
With all temperature reports for shipments now centralized, Salcobrand automated their report management and storage, leading to more efficient data handling and studies.
- Cost Optimization:
Salcobrand achieved a 50% reduction of costs associated with equipment acquisition and maintenance.
- Process Automation:
The time spent on preparing and receiving shipments with temperature control has allowed Salcobrand to save 2400 hours of work per year.
- Automatic Notifications:
The introduction of automatic notifications for temperature deviations has significantly improved response times, allowing immediate action by responsible personnel.
- Risk Management:
Salcobrand has mitigated the possibility of data loss and human errors. As from the first activation, Logmore data loggers are continuously recording data the temperature information is always accessible and thereby preventing any loss of products.
- Process Standardization:
Salcobrand has successfully standardized its procedures, eliminating deviations and ensuring consistent and reliable operations.
Overall, these advancements represent a significant leap forward in Salcobrand's supply chain efficiency, data management, and quality control.
"With the implementation of Logmore's data loggers, we ensure complete control of the cold chain, guaranteeing the delivery of our high-quality products." - Pharm. Sergio Correa, Coordinator of Regulatory Affairs at Salcobrand