How bioMérieux uses Logmore for automated QA reporting
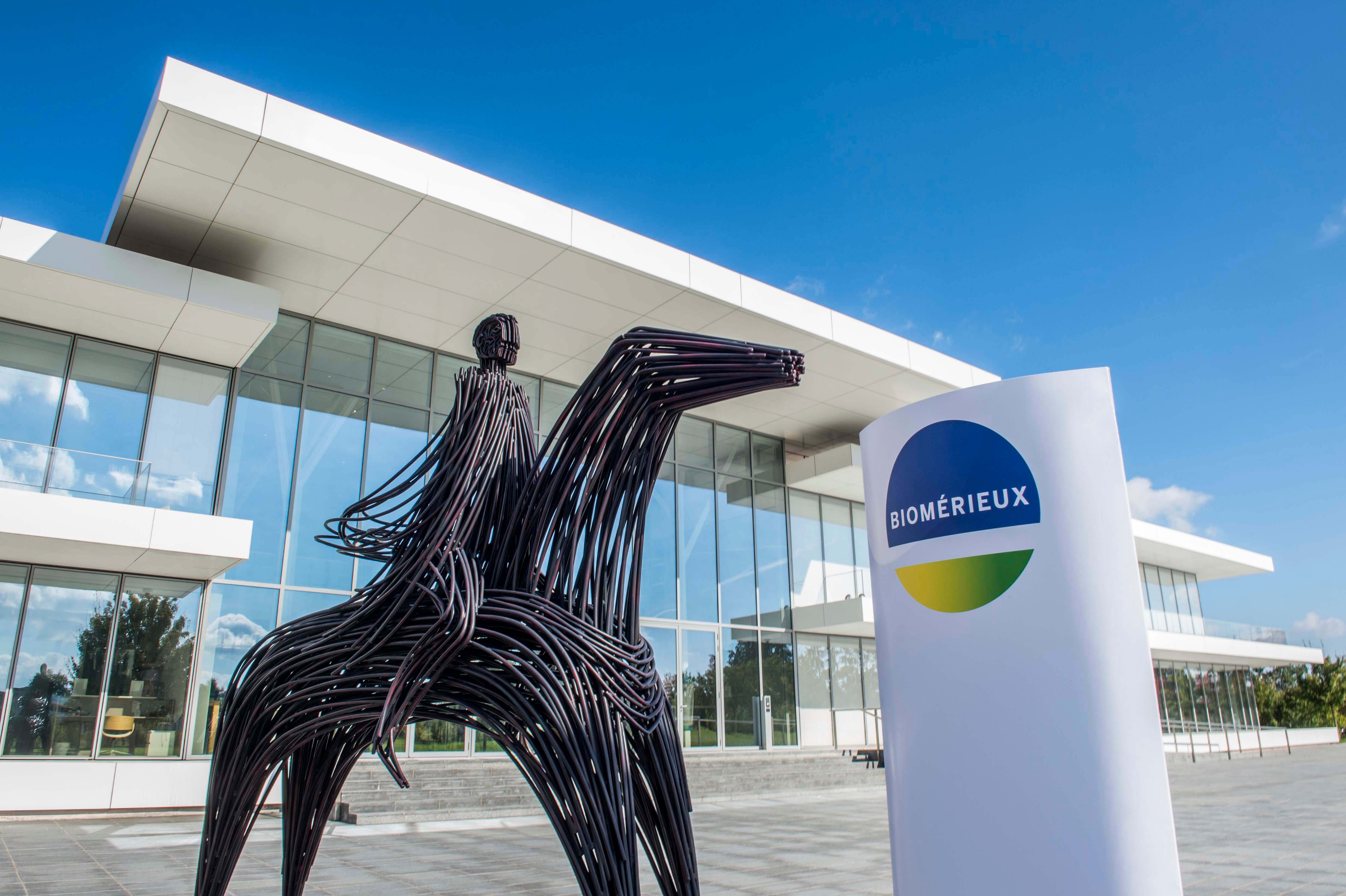
1.
Situation
As a world leader in the field of in vitro diagnostics for more than 55 years, bioMérieux is committed to fighting against infectious diseases worldwide. The company is present in 44 countries and is serving more than 160 countries with a large distribution network. In 2020, revenues reached €3.1 billion, with over 90% of sales outside of France, where bioMérieux was founded and is headquartered.
bioMérieux’s strategy is based on a long-term vision when it comes to its employees as well as to its outside stakeholders. Innovation and pioneering mindset are part of bioMérieux’s DNA and contributed to the Company’s growth throughout its history.
Being a leading company in the healthcare field, bioMérieux is convinced that being innovative is essential to meet public health challenges across the globe.
More information can be found at www.biomerieux.com
bioMérieux has always been driven by an unrelenting commitment to improve public health worldwide, and to lead the fight against infectious diseases.
Today bioMérieux boasts an impressive resume of 15 000 references of products distributed in 160 countries. Delivering such a large portfolio of solutions as well as respecting shelf lives and cold chain integrity are everyday challenges. bioMérieux aims to safely and timely provide the correct product to the correct end-user, and thus to offer the best customer experience. To achieve rapid lead times, storage and distribution models need to be top-notch. Keeping stock in optimized locations, and shipping the last mile from there with efficient solutions is a key to delivering reliably and efficiently.
Optimal service level requires to keep the inventory centralized as late as possible before deploying it to the end destination within the distribution network. As such, all subsidiaries and some distributors are replenished under VMI (Vendor Managed Inventory). This helps mutualize demand variations across the network, decreasing the risk of having back orders and shelf life issues.
Optimized locations and processes are also central to how bioMérieux works to reduce its environmental impact. The company aims to lower its greenhouse gas emissions by 50% by 2030, compared to 2019, and every step towards a greener future counts.
bioMérieux formalized a Corporate Social Responsibility (CSR) ambition that is an integral part of its strategic roadmap.
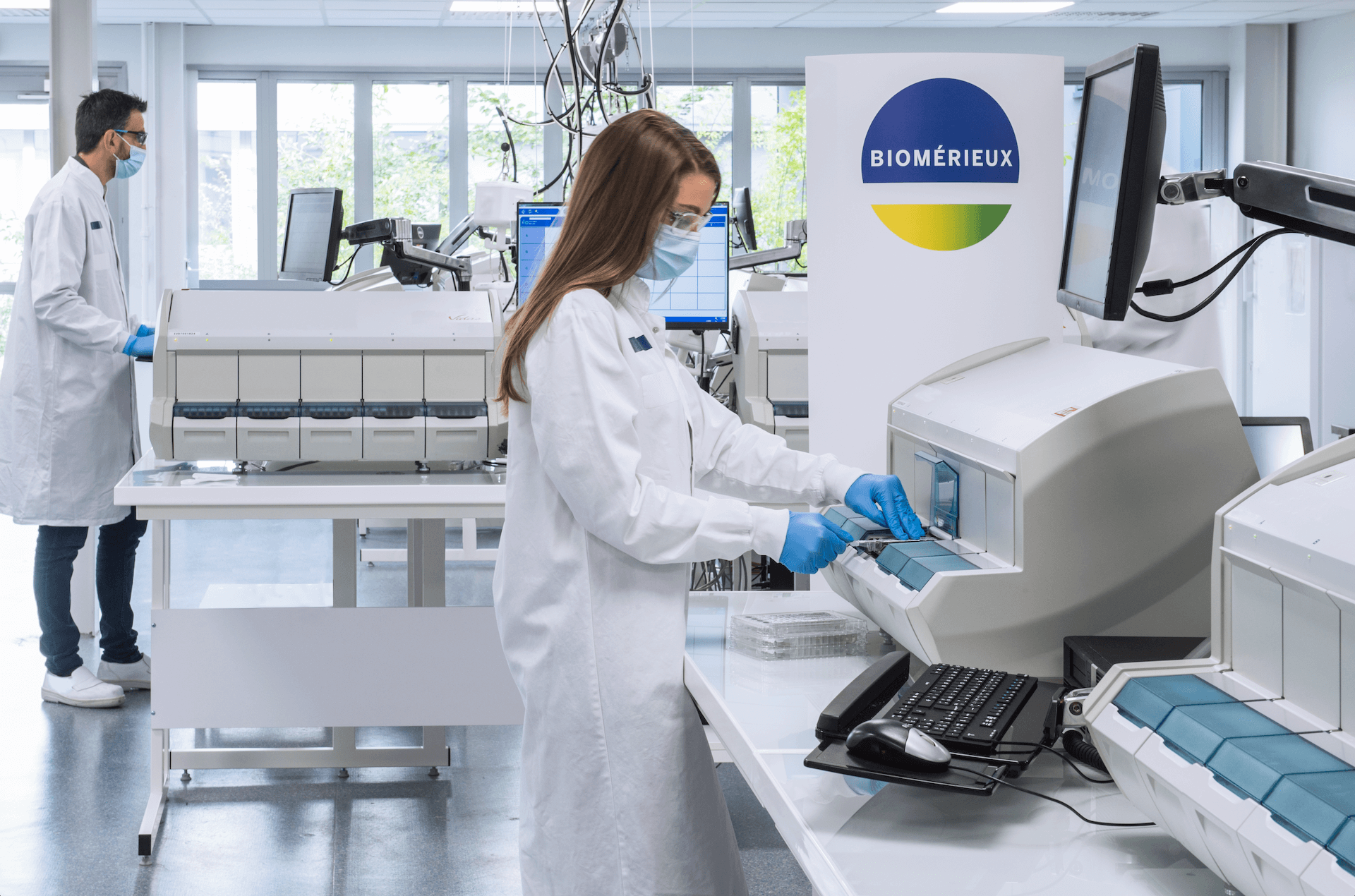
COVID-19 hits and new processes
Because of the COVID-19 pandemic, airfreight and ocean freight lacked capacity which impacted logistics activities all over the world. bioMérieux rapidly found alternative solutions and shifted a part of its production capacity to deliver large quantities of PCR tests for COVID-19. To provide the essential support to its customers and partners likewise, the company managed to ramp up production quickly. The COVID-19 situation has accelerated the action plan for increased reactivity, and agility conceived before the pandemic.
The company now builds sustainable business continuity plans with its partners. Standardization and simplification of the processes bring new value to the distribution anddigital innovations remove repetitive tasks that can be automated, so that partners and customers’ experience can be leveraged.
Goodbye to time-consuming processes
Two years before the cooperation with Logmore, a specific need was expressed by bioMérieux teams: they required the milestones of their shipments, superimposed on the temperature curve.
Back then bioMérieux was using the standard technology used by healthcare companies all around the world: USB data loggers supported by data reports exchanged by emails. The system was a demanding, time-consuming process for its logistics quality assurance. Not only did the solution using USB data loggers require bioMérieux to educate and onboard its own employees to use the devices, but also its consignees, subsidiaries, and direct customers as well. With the expansive distribution chain covering 160 countries, the scale of training was simply not feasible in the long run, with every new customer and partner needing individual onboarding.
Given the various types of organizations existing withconsignees, distributors, subsidiaries, and customers, bioMérieux encountered considerable challenges. Starting new partnerships took a lot of time, creating a bottleneck due to the amount of resources needed.
The bioMérieux Quality teams also faced a repetitive task that could soon be automated: manual analysis of the data. When asked if bioMérieux’ quality assurance could find out what percentage of shipments monitored by previous solution was failing to deliver data Juan Angel responded:
"No, I can't [find out the data integrity of the previous solution at this point] and I will not be able to find out, because we did not have a cloud like now with Logmore where we can see everything."
Valuable time was lost constantly due to the challenges in training, communication, and data retrieval. Regardless, the solution chosen in 2017 was implemented as it was the most commonly used one in the industry at the time... In 2020, bioMérieux launched an request for quote (RFQ) to simplify the process at the shipment recipient’s end by implementing something that would be extraordinarily easy to use.
“The goal was to get something easy, not rocket science”, says Alexis Monier, VP of International Logistics at bioMérieux
Alexis saw that the consignees should not have many difficulties.
The story of bioMérieux and Logmore’s cooperation began in 2020, when Logmore’s then-COO, now CEO, Niko Polvinen presented Logmore’s solution at DHL Innovation Center in Germany. Without the presentation of Niko at the DHL innovation challenge, bioMérieux would still be using its former loggers.
2.
Solution
The RFQ yielded multiple competitive offers from existing solutions on the market. The majority came from USB logger providers, all of which were described quite similar with each other. Other offers were for loggers using SIM cards, which also was not what bioMérieux was looking for. As Alexis said, the solution had to be easy to use for all parties involved.
The initial lead time for data retrieval and processing was set to be between 14 and 72 hours. Depending on air freight’s own lead times, these lead times were frequently doubling or even tripling, causing unnecessary delays.
There was a giant disproportion between the rapid lead times provided by the airlines to deliver the goods, and the quarantine time needed to process the temperature data. At this point, quarantine decreased the core benefit of airfreight.
Logmore – young yet capable
bioMérieux calculated the cloud-based Logmore solution to be considerably more helpful to combat the slow data processing times, cutting down the time products would spend in quarantine for quality assurance reporting purposes.
The Logmore Guardian also weighed 75% less than the other solutions and are reusable, reducing significantly the amount of electronic waste. For companies as expansive as bioMérieux and its shipment volume, using smaller, lighter loggers would add up to have a great impact, which would also be in line with the company’s vision of a greener, more sustainable future.
While all the things were right on paper, bioMérieux still had to make a calculated decision. Although Logmore was already working with DHL to secure COVID-19 vaccine deliveries, the company was still young. bioMérieux faced the doubts of whether a young company like Logmore had the ability to work within the healthcare industry on this scale. It was clear to bioMérieux that they would be the first major player in its field to implement Logmore in such a large scale – would Logmore be able to deliver the volume of loggers needed, and could they scale up on both hardware and software as needed? bioMérieux’s teams knew they were taking a risk, but it was calculated and it paid off.
Thorough preliminary testing and due diligence into Logmore proved the company was capable of delivering what was agreed on despite its young age.
Onward to victory
Challenges usually appear in early times. However, to Alexis’ surprise, he did not receive any comments or very little related to the communication between bioMérieux and Logmore all through the preliminary testing and launch project. During the planning, everything was fine, and no roadblocks emerged.
"This case has taught us a lot. We've cultivated a great relationship with the bioMérieux team, and received many useful insights from them. With those insights, we've further increased the Logmore Cloud functionality for the life sciences industry at a very rapid rate in such a short time", says Ilkka Pättikangas, the software lead of the project from Logmore.
The successful planning was due to the fact that both bioMérieux and Logmore were able to place knowledgeable people in charge of the project. On bioMérieux's side, there was never any need to implement a strong structure around the project. The discussions between the companies were straightforward throughout the project.
“I would love to see all the projects being handled like that”, Alexis mentions.
The transparency in the discussion was one of the keys to success. Every committed action was followed through, and all their doubts that had previously existed, disappeared as they saw that Logmore held promises.
3.
Results
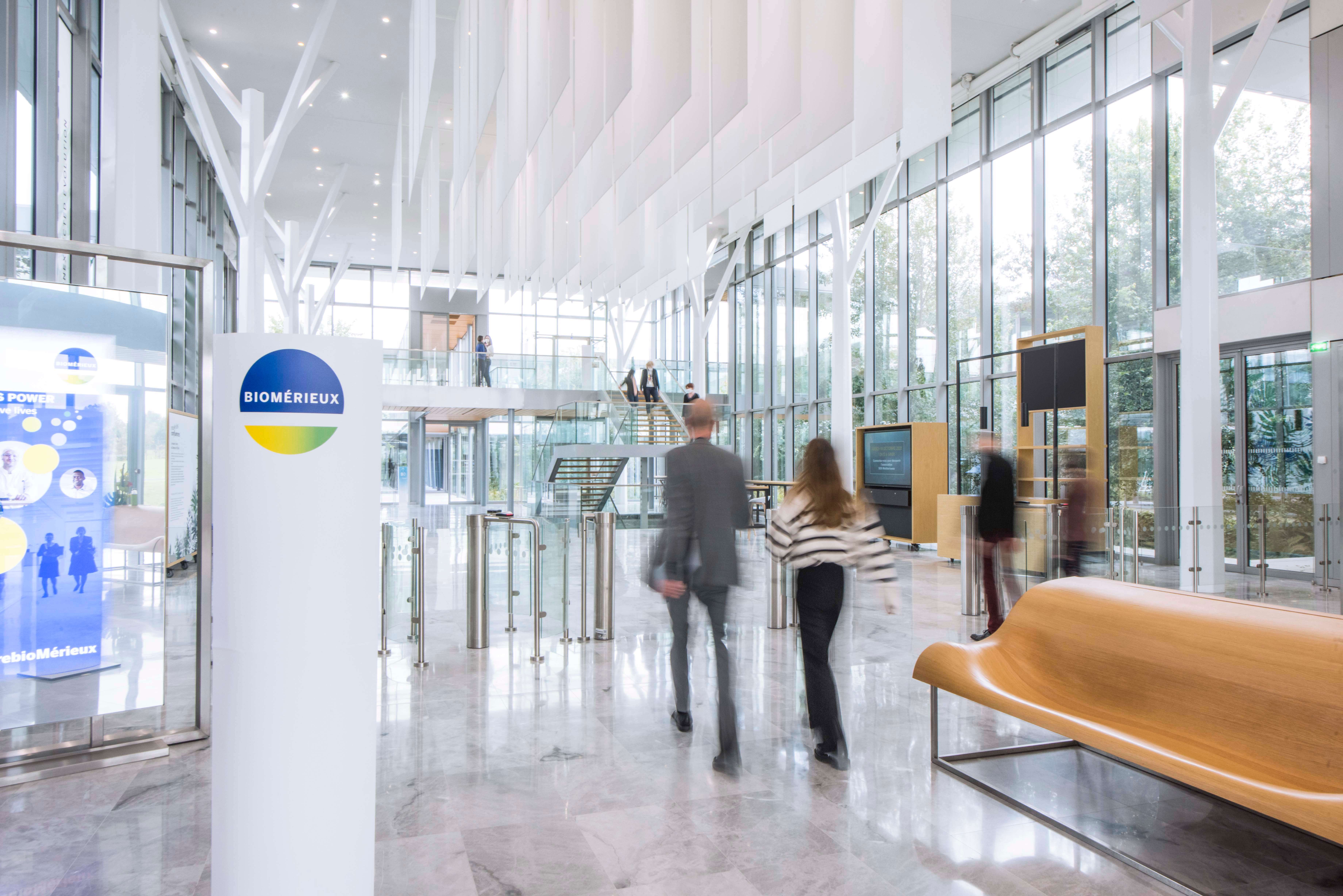
bioMérieux managed to deploy the Logmore solution in a record time without adding any extra resources, which came as a surprise to most people who had lived through the implementation of the previously used solutions.
The operational teams were happy to welcome the visits by the Logmore project team, developing a strong appetite for streamlining the processes. Especially the people working in the international distribution center were enthusiastic, and welcomed Logmore and the change the company brought. Most notably, the visits were rare: in the 3 months the initial project took, only 4 visits to the bioMérieux premises were needed. The rest of the implementation could be managed completely remotely, showcasing the ease of implementation and use.
Thanks to Logmore, bioMérieux has already been able to optimize their deliveries to demanding locations. Based on the data collected, they have changed the routes that go via Doha airport to instead use Singapore for deliveries bound to Australia. The combination of high temperatures and used handling processes in Doha have recently been shown to leave shipped packages to stay too long on the hot tarmac, potentially causing considerable waste and losses.
“The solution is the most cost effective solution on the market, without even explaining the benefits of the automated quality assurance process. Our quality teams see a 25% reduction in workload thanks to the automated temperature analysis, and the applicability of the service to any freight forwarder or carrier,” Alexis lists how bioMérieux already benefits from Logmore
As the solution is impacting 90% of its sales, bioMérieux could not imagined having such a positive outcome.
“The cooperation has already generated potential new opportunities, and shown places where we can improve in the future.”
Photos © bioMérieux / Noël Bouchut