14 Do's and Don'ts in Supply Chain Logistics
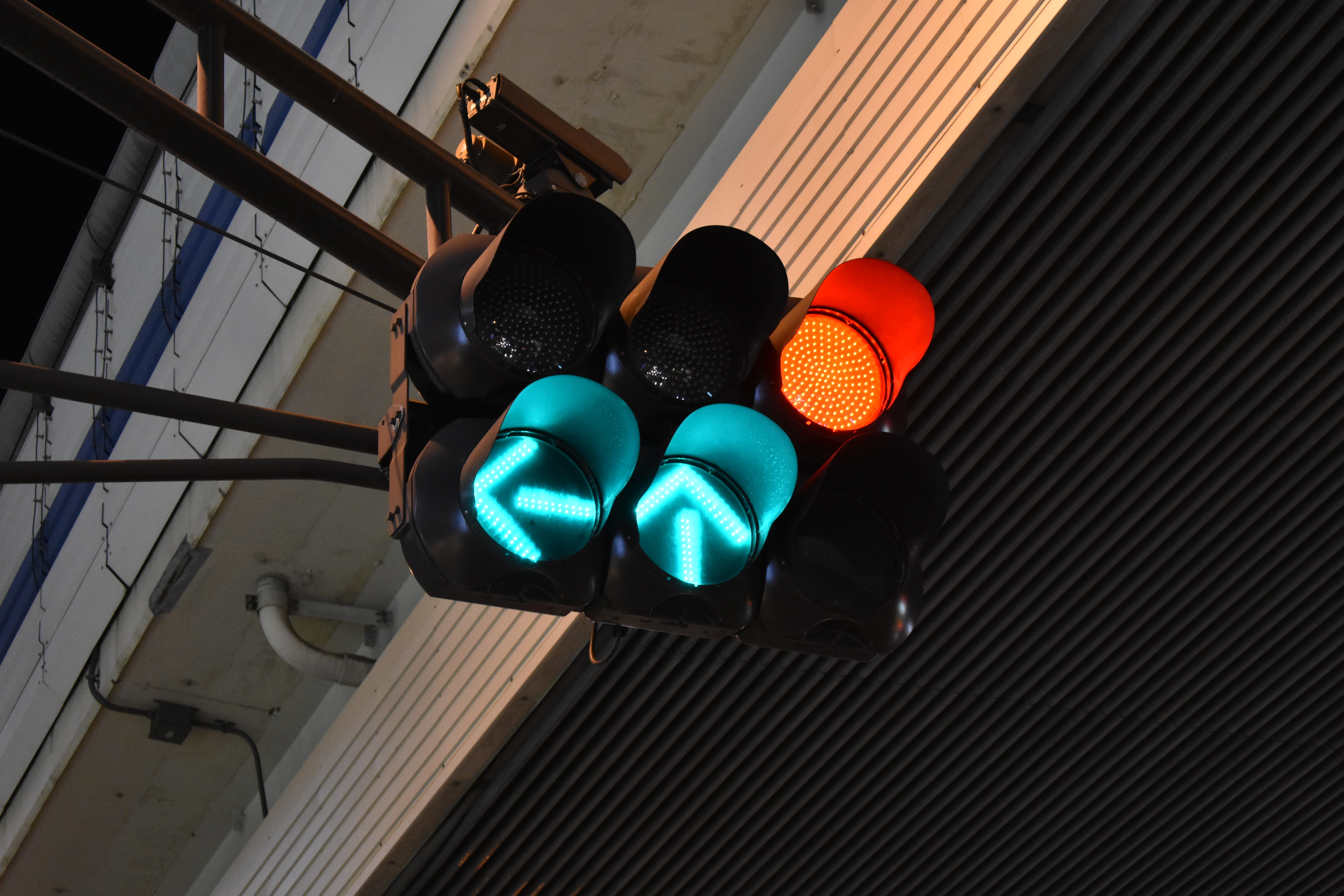
When reliability and speed are crucial, supply chain logistics can be the difference between a company thriving or withering away. Efficient supply chain logistics means faster, more predictable shipping that reduces costs and inventory while increasing revenue and customer satisfaction.
With so much at stake, it’s easy to overlook logistics as an afterthought. However, ignoring this aspect of business can lead to inefficiency, inventory issues, and other problems that will surely jeopardize your company’s success.
In this article we’ll go over some do’s and don’ts that can help you avoid the most common supply chain pitfalls.
1. Do: Be Proactive
If you’re not proactive about your supply chain, then issues can easily creep up and undermine your entire operation. Being proactive will allow you to put systems and processes in place to minimize downtime and disruptions, and to identify and solve problems before they become bigger issues.
Be proactive with your procurement and inventory management. This will help you identify issues in your supply chain and address them in a timely fashion. Keep an eye out for potential problems, such as rising inventory or increasing costs, or issues with certain carriers or suppliers. If something seems off or if you notice an increase in certain problems, then it’s best to address them as soon as possible.
2. Don’t: Skimp on Pre-Shipment Inspections
All too often, companies cut corners with pre-shipment inspections in an effort to reduce the overall cost of logistics. What they may not realize is that cutting corners here will end up costing them in the long run. Inspections identify any issues with your goods before they’re shipped, giving you the chance to switch suppliers if there are major issues.
Without inspections, you’re at risk of receiving goods that don’t meet your specifications, which will have to be rejected and repurchased. This can create major inventory issues that will affect your cash flow and customer satisfaction.
Inspections also help you identify risks to your supply chain. If your goods are coming from a country known for corruption or political issues, an inspection report could allow you to decline the shipment. This could end up saving you from future issues, like delayed or missing shipments.
3. Do: Determine Your Company’s Core Business Strategy
As the first step in optimizing your supply chain logistics, you need to get crystal clear on your company’s core business strategy. What are your core values? Where are you hoping to focus your efforts and energy? What are the goals you’re trying to achieve? To get the logistics side of your business in order, you need to understand what the other functions are bringing to the table.
Once you understand the other functions and processes within your company, you can work to optimize your logistics to work in harmony with them. You can also use your company’s strategy to determine which logistics providers might be best suited for your business. Look for providers with experience in industries similar to yours, as they’ll likely have an easier time understanding your business’s logistics needs.
4. Don’t: Rely Solely on Data for Supply Chain Decisions
While data is an extremely important part of the supply chain process, relying solely on data will almost always lead to suboptimal decisions. In some scenarios, the data will be available to you, but in many others, it simply won’t be. You need to take into account the people involved in the supply chain process and how they’ll respond to different scenarios.
Will your employees be able to handle the volume? How do the weather and other outside factors affect your shipping routes? What about your customers? Will they be able to receive shipments on their requested timelines? Are there any other external factors that might affect your customers? These intangibles can’t always be calculated, but they still need to be factored into your decision-making.
5. Do: Be Realistic About Timing and Costs
When your customer places an order, they expect it to be fulfilled. In many cases, they also expect it to be delivered on a specified date. Your logistics operations need to be able to deliver on those expectations without fail.
It’s important to maintain realistic expectations about how long it will take your team to deliver this product. If you consistently promise unrealistic timelines, your business will lose credibility. This could lead to fewer sales, as customers will likely understand that delivery dates really are just guesses.
Similarly, it is essential to be realistic about the costs of your logistics operations. Customers will want to know how much they will be charged to receive the product they ordered from you.
It’s important to ensure you have a firm grasp on the costs associated with your logistics operations to give your customers an accurate price estimate. If you consistently promise low prices that you can’t deliver on, customers will have little reason to continue doing business with you.
6. Don’t: Reinvent the Wheel When Looking for a New Solution
Yes, you need to be selective about the technologies you implement, but don’t go overboard and reinvent the wheel every time an issue arises. Instead, look for existing, tried, and true solutions that will get the job done without disrupting your company’s operations too much.
A good example of this is an inventory management system. If your employees are manually recording inventory levels and you’re experiencing issues with inaccuracies, you may want to consider investing in a barcode scanning system that will record the data for you.
7. Do: Put Equal Effort Into People and Processes
You can implement the best technology in the world, but it won’t matter if your people aren’t equipped to utilize it effectively. You can have the most efficient supply chain and logistics process in the world, but it won’t matter if your employees can’t execute it correctly. You need to make sure you’re equipping your employees with the tools, training, and support they need to make the most of your logistics process.
If your employees don’t understand what their responsibilities are, they won’t be able to execute the process properly. You also need to make sure your employees have the right attitude and mindset. You can’t expect them to be as invested in their jobs if they aren’t happy.
8. Don’t: Underestimate the Importance of Communication and Collaboration
One of the most common issues in supply chain operations is a lack of communication and collaboration. This can happen between different supply chain partners as well as within your company. If there is any type of miscommunication between supply chain partners, it could lead to problems in your supply chain operations.
For example, if the manufacturer and the distributor don’t communicate the products could end up arriving at the wrong place, or not arriving at all. Whenever possible, you should strive to conduct business with partners who value communication and collaboration.
9. Do: Have a Reliable Measurement Program in Place
Logistics professionals depend on metrics to help them make decisions and improve operations. To make sure your data is accurate, however, you need to have a reliable measurement program in place. This means taking the time to properly define your metrics and selecting the most suitable measurement systems.
A measurement system’s accuracy is dependent on how well it reflects the processes and activities it’s supposed to measure. A good measurement system will help you identify areas of improvement, make better decisions, and increase the likelihood of achieving your business goals.
10. Don’t: Be Afraid to Shake Things Up If Something Isn’t Working
On the other hand, if you’ve implemented a solution and it’s still not producing the results you want, you don’t have to stay with it. You need to be careful when making changes to your logistics processes and solutions, but if something isn’t working, you have to shake things up.
You may find that you’ve implemented the solution incorrectly, or perhaps the solution itself isn’t working. If this is the case, you need to find a new solution that does work. You might want to try a different technology or process. You might want to hire new employees. You might even want to change your company culture. Although these solutions may seem drastic, they’re necessary in some cases.
11. Do: Make Sure Your Packaging is Up to Snuff
When it comes to supply chain logistics, the packaging is just as important as the shipping method itself. If you’re shipping fragile items in boxes that are inadequately reinforced, you could damage your items and ruin your customer’s experiences. You need to make sure your packaging is up to snuff.
Not only should you make sure your packaging protects your items, but it should also be easy to use and reuse. You don’t want to be constantly buying new packaging, and you don’t want to be wasting time on it either. You should also keep an eye on the competition and on emerging trends in your industry. If you notice one of your competitors using better packaging, you should consider switching as well.
12. Don't: Forget to Manage People and Culture
You also need to pay attention to the people and culture within your company. As we’ve already discussed, the logistics process is a people-driven process, so you need to make sure your employees are happy and engaged. You also need to make sure that your company’s culture is conducive to success.
If you’re experiencing problems in terms of productivity, morale, or engagement, you may want to look into solutions such as employee engagement surveys to improve your culture and logistics process. Logistics is a complex process that requires careful planning, collaboration, and attention to detail. Although it may not be the most glamorous part of your business, it’s one that can make or break your company.
13. Do: Leverage Technology to Improve Efficiency and Accuracy.
Technology’s ever-growing influence on supply chain operations has led to increased efficiency and productivity throughout the field. There are several fields that technology has had a huge impact on, including inventory management, shipping, and logistics.
In logistics, technology helps with the efficient planning and tracking of shipments, providing visibility and transparency to the entire operation. This means fewer delays, fewer errors and miscommunications, more accurate information, and ultimately a smoother operation.
14. Don’t: Rely Solely on Technology
While technology is important in supply chain logistics, it is not the solution to all of your problems. Technology is important because it helps you to understand your supply chain. It allows you to collect and analyze data, which can help you identify where your supply chain is lacking. From there, you can prioritize which areas of your supply chain need the most improvement.
However, relying solely on technology can be dangerous. For example, relying solely on technology to track inventory can create an inaccurate picture of your supply chain. This is because you likely won’t have the same level of detail for your inventory as you do for your shipments. In this case, you would have a clear picture of where your shipments are, but a less accurate picture of your inventory.
Conclusion
When it comes to supply chain logistics, you need to make sure you’re doing everything you can to be as sustainable as possible. This can mean making changes to improve operational efficiency, partnering with new providers, or even switching up the types of carriers you use.
Don’t assume everything is good when it comes to logistics. Instead, be proactive and continuously evaluate and adjust based on ongoing feedback. Finally, don’t underestimate the importance of communication and collaboration both within your company and with your supply chain partners.
By following these do’s and don’ts, you’ll be well poised to optimize your supply chain, making your operation more reliable and sustainable, while avoiding the most common pitfalls that can derail your business.