From Damage Control to Prevention, Prediction and Optimization
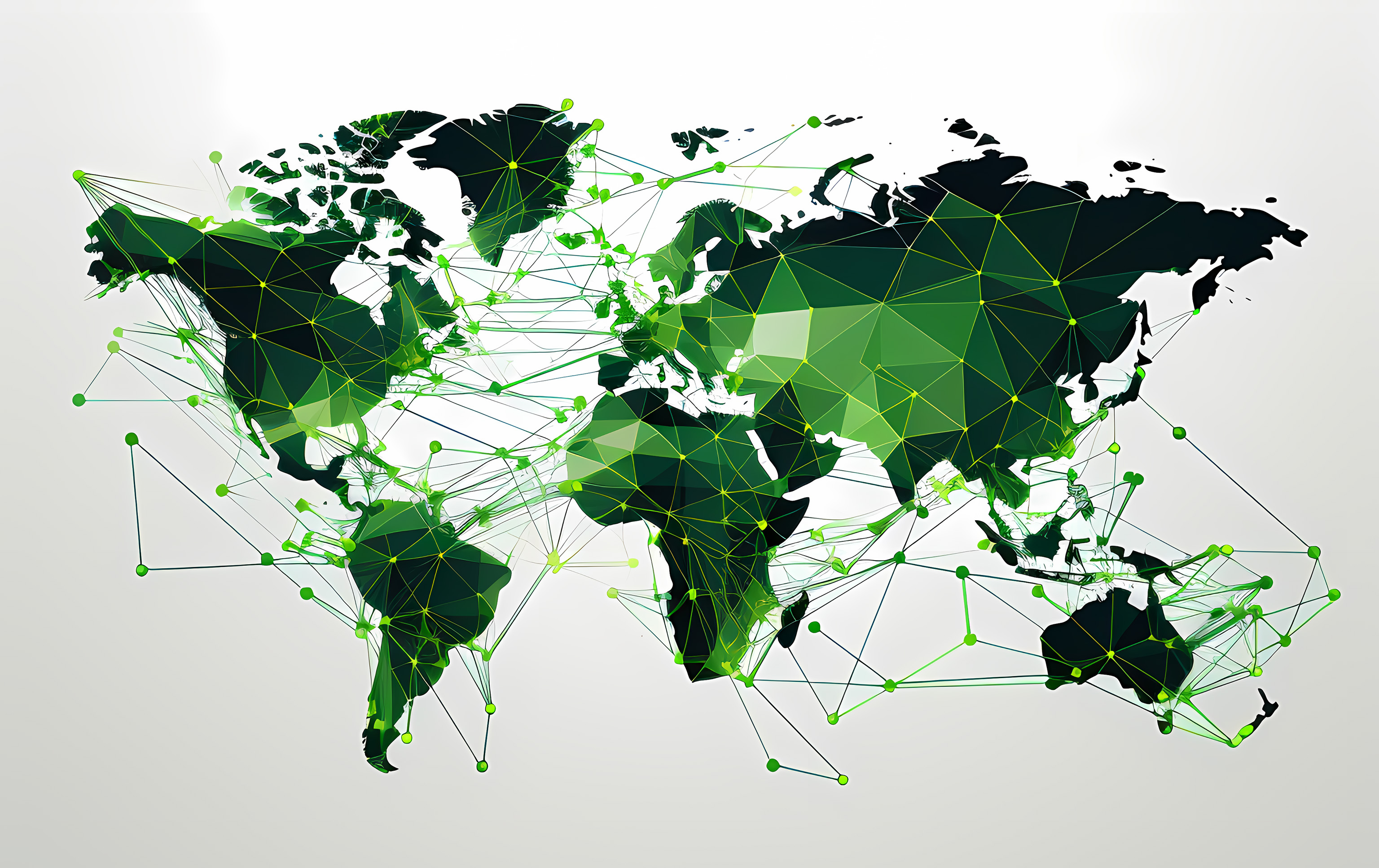
Current focus: Coping with the issues that already happened
The regulation sets stringent requirements for the quality assurance when transporting pharmaceuticals, and increasingly also for handling perishable food. The primary intention of regulation is to guarantee that the transported products are safe to consume, and as a result the focus of the quality operations has always been to identify potential risks.
Traditionally the typical procedure has been to monitor the transportation conditions, and to reject the shipment, in case there is any deviation from the rules. Currently used technology is providing tools specifically for identifying problems and deviations: USB data loggers monitor the temperature and alert in case some pre-set threshold has been exceeded. Often this means discarding all the goods in the shipment - or even in the best case - a lot of manual work to select which individual product items can still be used safely.
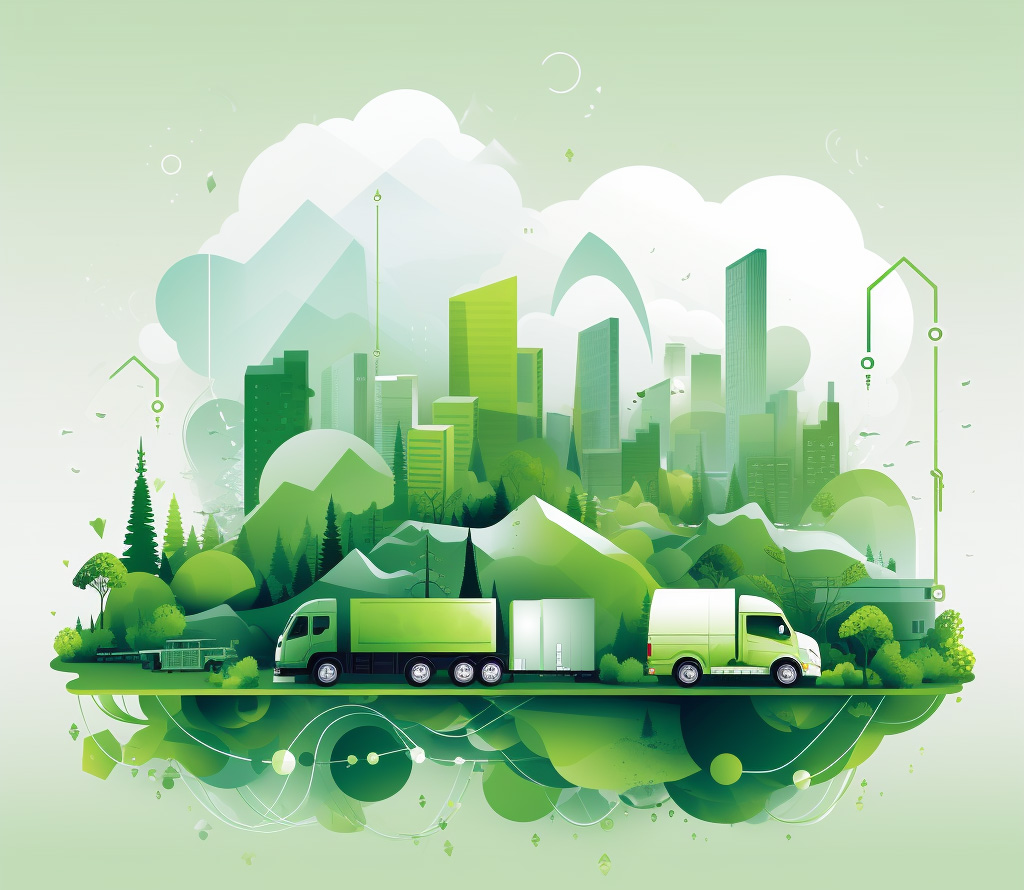
Improve sustainability with more insightful data
However, all the rejected goods contribute to the massive amount of waste accumulated: Globally 50% of all vaccines and 30% of food ends up being spoiled. In addition to securing product safety by identifying issues that already happened, the logistics industry needs to increasingly aim to predict and prevent them in advance.
Global logistics of sensitive goods is a complex domain, with a lot of uncertainties and several stakeholders that typically have only a limited visibility on the e2e supply chain. Therefore no single company or technology solution alone is able to provide a silver bullet to address the issue. Still, here are a few approaches to help solve the challenge.
1. Collect, aggregate and leverage all the available data
The focus on handling issues, for instance shipments with a temperature deviation, has led into traditionally collecting and storing data specifically on those exception cases. In case a USB data logger has indicated an alert, the data has been stored locally and used to decide on the next action for the respective shipment.
This helps to ensure that the potentially unsafe goods are not distributed forward, but collecting data only on exceptions gives a very incomplete picture of the overall situation. In certain cases this can also cause wrong interpretations, similarly to the classic case of survivor bias.
Instead, collecting and aggregating data from all the shipments puts the exception cases to context and allows analyzing the big picture. Also collecting data frequently or real-time during the transportation improves the visibility. In order to pro-actively optimize the logistics and to prevent waste, it is helpful to look at the for instance the following aspects:
- How do the failed shipments compare to the successful ones, in terms of length, season, origin, destination etc.?
- What trade lanes and routes cause a disproportionate amount of problems?
- Which of the used logistics providers on average have the least issues?
- What location, leg or phase of the journey is the critical phase?
- What are the identified patterns that precede an alert being activated?
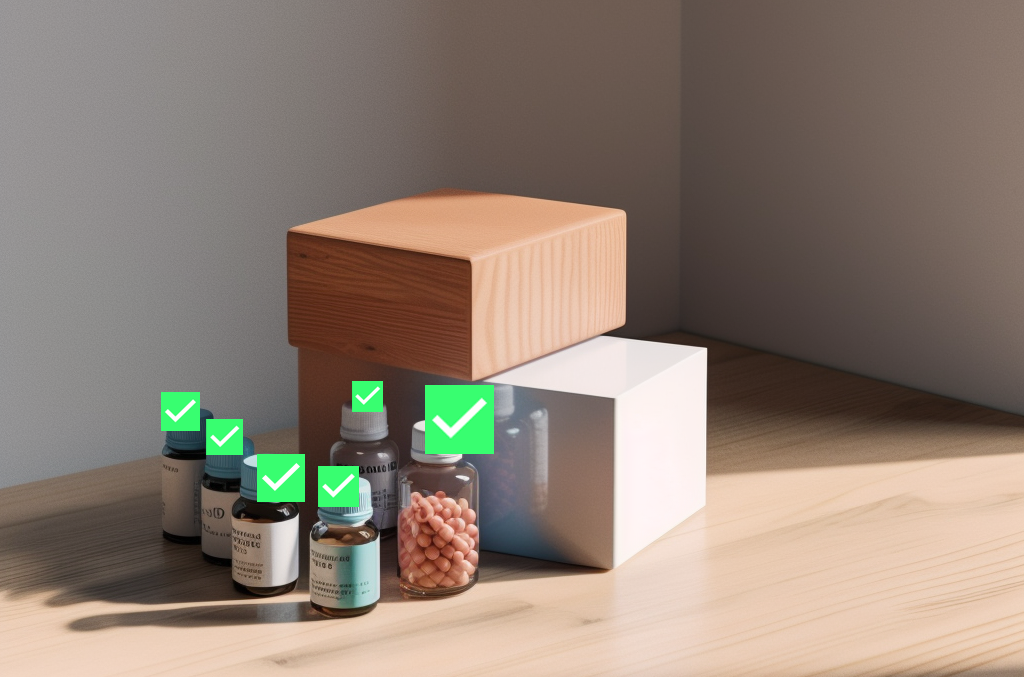
2. Collect data on the product level, for the whole journey
Monitoring conditions of a shipped package or pallet often leads to making decisions based on the worst case scenario. There are two primary reasons for this.
First, often shipments include several types of products, allowed to stay in different temperatures for different time intervals. The alert rules of the shipment need to be set based on the most sensitive products, and in practice the whole shipment needs to be stopped, in case these most stringent thresholds are exceeded. To prevent throwing also completely valid goods away, the logical solution would be to monitor the goods on a more granular level - eventually having relevant alerts specific to each product-type and immediately making correct quality approval decisions for them.
Second, monitoring on shipment level tends to leave substantial visibility gaps along the journey. Even if the transportation leg between the shipping location and consignee’s warehouse is tightly monitored, there is seldom data available about the storage conditions before the shipment or how the goods were handled after receiving. When the measurement data is missing, the overall assessment needs to be based on assumptions. To be on the safe side, the product shell-life is typically determined by assuming the worst case scenario. If we would have real condition measurement data available instead of the arbitrary worst case assumptions, the best-before dates could be extended and plenty of waste prevented.
3. Indicate what to do next - not just alert on incidents occurred
The tools currently on the market, like data loggers and time-temperature indicators, do show alerts when certain conditions have been exceeded. However, at this point it is typically already too late to save the shipment of goods. To have a chance to still react and optimize the process, the people handling the shipment would need more forward-looking information on how much time there is still left and what conditions need to be met, to prevent spoiling of the transported goods.
Achieving a more sustainable supply chain will require condition monitoring products that help make better decisions on the spot, for instance by indicating the still available time the transported products can be in certain temperatures and by providing instructions for correct handling of the goods.
New technology to help planning ahead
Predicting issues in advance, in order to take the correct preventive actions, will require adapting processes and also new tools. That is what keeps us busy in Logmore developing for instance:
- Connected data loggers that aggregate all condition monitoring data to Cloud to enable analytics both for quality and logistics optimization
- New types of small connected temperature indicators that make it feasible to radically scale up condition monitoring for the whole logistics journey from manufacturing to the final end-user, down to the level of individual products.
- Condition monitoring solutions that - besides excursions of predefined alert rules - give the consignee plenty of additional information e.g. about the remaining “stability budget”, i.e. how long the product can still stay outside of the defined temperature ranges.
We firmly believe this is a massive opportunity to prevent waste and make supply chains more sustainable.