7 Tips to Improve Warehouse Efficiency
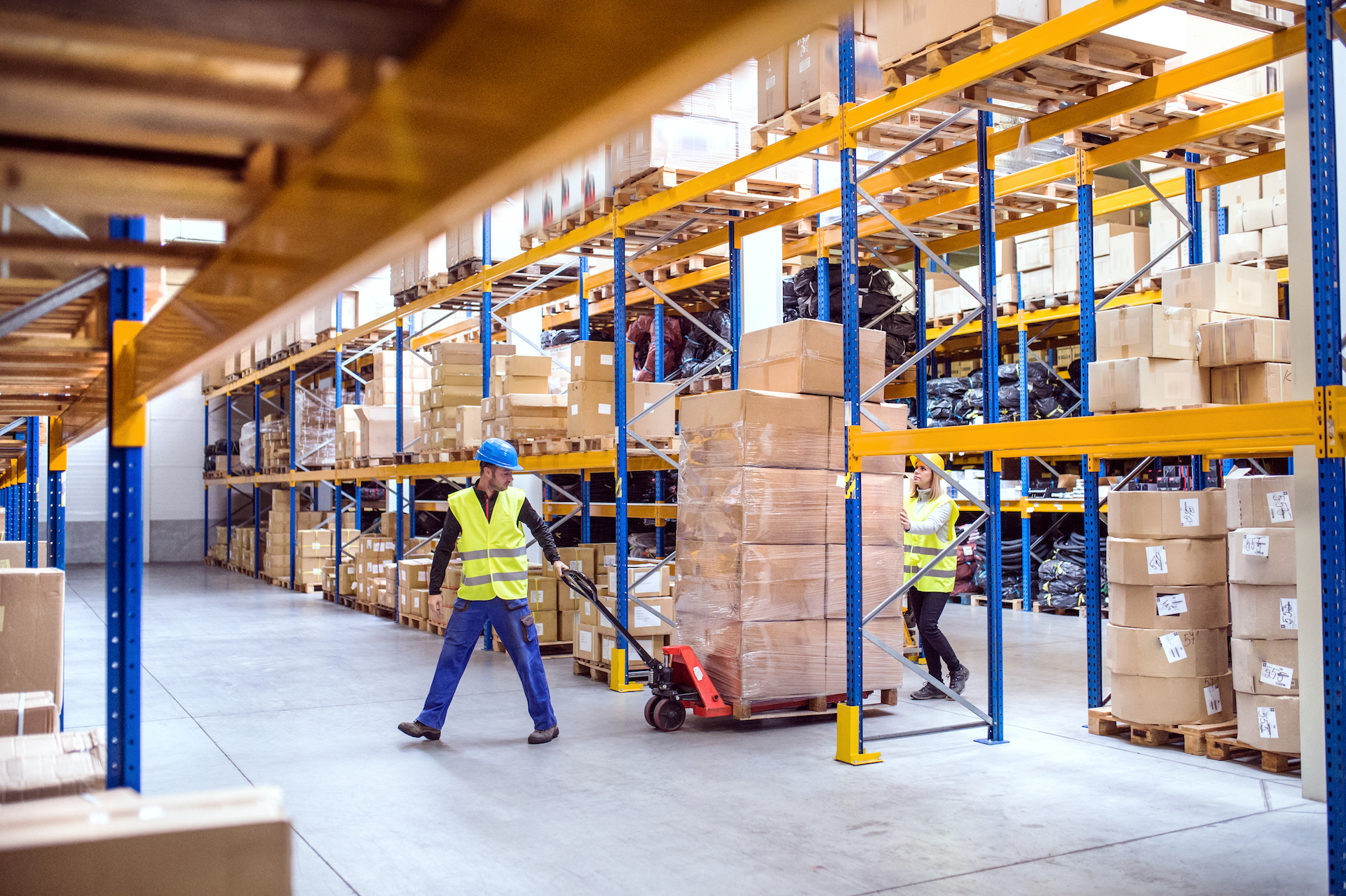
Unfortunately, saying you want to enhance efficiency versus actually doing it are two completely different things. In fact, your company can fully commit to efficiency and waste prevention initiatives and come up short. Why? Because while many organizations might have their hearts in the right place, they’ve committed to ineffective methods. Or they went forth with something that may work for another business, but not their own. At the end of the day, every warehouse in existence has its own unique infrastructures, nuance, and even culture.
Yes, there have been tremendous strides in warehouse efficiency. Namely, due to logistics techs like automated robots, AI, machine learning, and warehouse management software, for instance. However, it’s not the simple act of implementing these tools and processes that’ll prevent those distinct areas of weakness from muddying up the works. It’s through looking at the methods and strategies discussed below with a keen eye and weighing where your warehouse needs improvement that you’ll experience enhanced efficiency. Beyond that, you must consider how you can implement these strategies and at what cost.
Now that we’ve provided something of a disclaimer, let’s examine how to improve warehouse efficiency:
1. The powerful allure of incentives
Interestingly, our first tip for bolstering efficiency in your warehouse has nothing to do with the immensely powerful technologies of the day. Nope. It’s through old-fashioned performance incentives that you’re bound to get the most results when it comes to shoring up weaknesses in the warehouse.
While there should be a level of difficulty to these incentives, they can’t be unobtainable. However, receiving this incentive should still be based on doing exemplary work—only don’t expect the impossible. It’s all about finding the middle ground between something your staff can do in their sleep and something that’d require them to work 20-hour days.
2. Measurement is paramount to success
There’s an old saying about how you should only aim to be better than you were yesterday.
There’s a lot of merit to that notion. Still, it’s virtually unfathomable to be better than you were yesterday when you don’t have a frame of reference or comparison. More specifically, you require the correct form of measurement in your warehouse to paint an accurate picture and know where you’re succeeding and need improvement.
One way in which warehouses are measuring efficiency and performance is through enterprise resource planning (ERP) systems. They’re able to calculate how long it takes to perform an operation.
Though a standard measurement needs to be calculated with a sampling method or time study. Once these measurements are agreed upon, the ERP can be implemented with great success.
3. Cycle counting as a form of quality assurance
One of the quintessential techniques used in inventory management is something known as cycle counting.
In performing cycle counts, you’ll gain a peak – real-time – into inventory. Also, cycle counting regularly enables warehouses to integrate different systems and technologies that’ll predict demand.
Yet, cycle counting goes one step further than just forecasting demand and other such benefits. It is an ideal quality assurance test because the process can be utilized to validate products ordered versus shipped to assess workers and procedures, etc.
4. Embracing a comprehensive WMS
A WMS is an incredibly valuable facet of warehouse efficiency, primarily if it is reliable and robust. Remember though, the WMS is merely one system.
Your warehouse requires the vastest, most well-rounded WMS that can work in harmony with other systems across the supply chain. This includes systems involving transportation management, warehouse execution, and brick-and-mortar retailers, etc.
5. Automate mundane tasks with robotics
Any process that’s redundant and monotonous should be automated in your warehouse.
Don’t get me wrong: spending frivolously on robotics to handle all aspects of work in your warehouse isn’t going to help with efficiency. Still, figure out the processes that should be automated—you’d be surprised at how many aspects of work would be improved.
There are several fantastic benefits with these technologies, starting with safety. Plus, while some may fear layoffs and the end of people with jobs, it’s really the opposite. Since robotics and automated technologies directly correlate with increased productivity and profits, people keep their jobs and flourish more. The nature of their work is different, as they focus on more high priority, nuanced tasks.
6. Keep processes as straightforward as possible
When a warehouse struggles with efficiency, in many cases, it stems from a multitude of unnecessary touches within inventory and order movements.
For efficiency to be at its peak in your warehouse, products must flow unencumbered from inbound freight to slots to the hands of pickers. Then they must end up in the box used for shipping and into the outbound truck.
This process is nowhere near as complicated as it sounds. And you’ll notice that once touchpoints have been filtered down to the bare minimum and costs decrease at an exponential rate. Beyond that, you’ll mitigate most risks within warehouse operations.
All these factors surrounding the reduction of touchpoints combine to drive efficiency and will have your warehouse running shipshape.
7. Fine-tune the overall warehouse layout
When it comes to mapping a warehouse for efficiency, you must contemplate the use of inside and outside space. To elaborate, truck drivers shouldn’t struggle to find parking, loading and offloading time should decrease, and operation costs should increase, etc.
Furthermore, when receiving goods, the area ought to be free of clutter. The least amount of time possible should be spent when delivered products are inspected and placed into slots.
One of the more common, successful strategies used in this regard is known as the FAST approach. Here’s a more comprehensive breakdown of that process.
With these helpful tips, you should have gained some keen insight into how to run your warehouse more efficiently.